
GPU technology in Ansys Fluent: accelerating the simulation instead of the wind tunnel
Sector: Automotive (motor vehicles/trucks)Specialist field: Fluid mechanicsWith the new Fluent GPU technology, 700 iterations with a mesh size of 30 million nodes can be carried out in less than 10 minutes – something that was once just a dream. Such computing times were previously only achieved with massive parallelization on a large number of CPU cores, with significantly higher costs and energy consumption.
Summary
Task
Semi-trailer units, with all attachments, must be certified in accordance with the guidelines of the European Commission with regard to their CO2 emissions and fuel consumption. The decisive factor here is flow resistance, which is determined by measurements in the wind tunnel or by calculations using CFD software.
Solution
By simulating the trailer unit, design changes can be quickly analyzed and evaluated. There is no need to create a real model and test it in the wind tunnel. This provides a clear advantage when designing the aerodynamics, as the cause-and-effect relationship is not always obvious.
Customer benefits
Development engineers at Krone can assess the flow resistance of their trailers using a wide variety of add-on parts available in the CFD software from Ansys, without the need for time-consuming and expensive measurements in the wind tunnel. Rapid analysis using simulation reduces costs and shortens development times.
Project Details
Task
For over 100 years, Krone has been committed to quality and innovation in its commercial vehicles. Today, semi-trailer units with all attachments – such as hubcaps and rear wings – must be certified in accordance with the guidelines of the European Commission with regard to their CO2 emissions and fuel consumption. The decisive factor here is flow resistance, which is determined by measurements in the wind tunnel or by calculations using CFD software.

Customer Benefit
Development engineers at Krone can assess the flow resistance of their trailers using a wide variety of add-on parts available in the CFD software from Ansys, without the need for time-consuming and expensive measurements in the wind tunnel. Rapid analysis using simulation reduces costs and shortens development times.
In addition, a new EU standard is currently being developed in which the certification obligations and regulations for determining the CO2 emissions and fuel consumption of heavy commercial vehicles will be based on numerical simulation software. Corresponding programs and generic 3D vehicle models will be made available in the future. Of course, trailer manufacturers who have been using simulation for a long time and can draw on extensive experience will have an advantage.
CFD simulations not only provide information for EU certification, given that the clear representation of the flow field gives designers important information on potential for improvement, they also enable so-called “dead zones” or areas with vortex separation to be reliably identified. The simulation allows a better understanding of the trailer's behavior and thus enables the identification of design measures to further reduce fuel consumption for the end customer.
The GPU solver in Fluent provides additional acceleration, meaning that the calculation results are available in a very short time. Due to the larger number of simulations at the same time, more extensive variant studies can be carried out, with which the design can be optimized in an even more targeted manner.
Solution
Krone relies on simulation with Ansys Fluent to determine drag coefficients. By simulating the trailer unit, design changes can be quickly analyzed and evaluated. There is no need to create a real model and test it in the wind tunnel. This provides a clear advantage when designing the aerodynamics, as the cause-and-effect relationship is not always obvious and even small changes in the reduction of flow resistance can lead to significant CO2 savings throughout the entire “trailer life”.
An additional benefit of using Fluent is that the meshing of poor geometries can be performed efficiently using the fault-tolerant workflow in Fluent Meshing, without having to repair the geometry beforehand. Even very large or finely meshed models can be quickly simulated with the new Fluent GPU solver.
700 iterations with a mesh size of 30 million nodes can be carried out in less than 10 minutes - something that was once just a dream. Such computing times were previously only achieved with massive parallelization on a large number of CPU cores. With the new Fluent GPU technology, this now happens on powerful graphics cards, with significantly lower costs and energy consumption.

Cover Image: © CADFEM
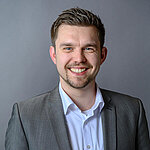